Keep Your Line Running Smoothly with Reliable Packaging Machine Repair
Keep Your Line Running Smoothly with Reliable Packaging Machine Repair
Blog Article
Quick and Reliable Product Packaging Maker Repair Service Provider to Decrease Downtime
In the affordable landscape of production, the performance of product packaging procedures rests on the dependability of equipment. Quick and reputable fixing services are important in mitigating downtime, which can cause considerable operational setbacks and economic losses. Comprehending the importance of timely treatments and the duty of professional specialists can transform just how services approach maintenance and repair services. Navigating the myriad options readily available for repair service services can be tough. What factors should companies think about to ensure they are making the right selection for their operational needs?
Relevance of Timely Fixes
Timely repairs of packaging machines are important for keeping functional efficiency and reducing downtime. In the hectic atmosphere of manufacturing and packaging, even minor malfunctions can lead to considerable hold-ups and efficiency losses. Addressing concerns without delay ensures that equipments operate at their optimal capacity, thus safeguarding the circulation of operations.
In addition, normal and timely upkeep can avoid the acceleration of small problems right into major breakdowns, which commonly incur greater repair costs and longer downtimes. An aggressive method to device repair work not just maintains the integrity of the equipment but also improves the total dependability of the assembly line.
Additionally, prompt repair services contribute to the longevity of packaging equipment. Makers that are serviced promptly are less most likely to struggle with extreme wear and tear, enabling organizations to optimize their investments. This is particularly crucial in sectors where high-speed product packaging is essential, as the need for consistent efficiency is extremely important.
Advantages of Reliable Provider
Reputable solution carriers play a crucial duty in making certain the smooth procedure of product packaging equipments. Their knowledge not only improves the effectiveness of repair services but also adds dramatically to the longevity of equipment.
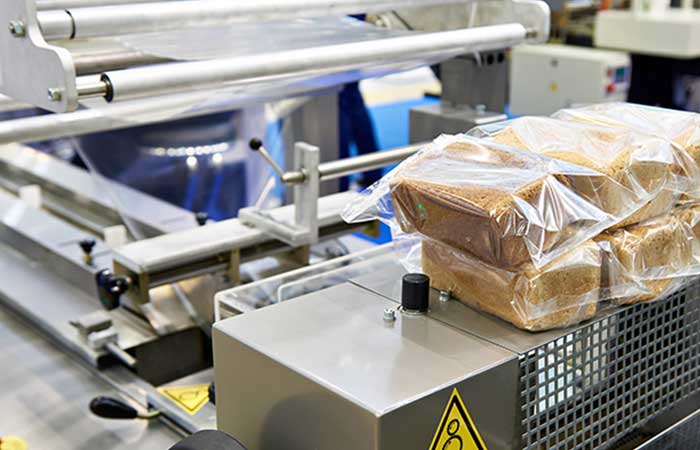
Additionally, a trusted provider provides extensive assistance, including training and assistance for staff on maker operation and maintenance ideal practices. This not only encourages staff members however additionally cultivates a society of safety and performance within the organization. On the whole, the benefits of engaging trustworthy solution providers expand beyond immediate repair services, favorably impacting the whole functional operations of packaging procedures.
Typical Product Packaging Maker Issues
In the world of product packaging procedures, numerous concerns can compromise the performance and functionality of makers. One prevalent trouble is mechanical failure, typically coming from wear and tear or poor upkeep. Elements such as motors, gears, and belts might stop working, leading to failures that stop manufacturing. One more usual concern is imbalance, which can cause jams and uneven product packaging, affecting product high quality and throughput.
Electric troubles can likewise interrupt packaging procedures. Malfunctioning electrical wiring or malfunctioning sensors might cause irregular maker actions, creating hold-ups and increased functional costs. Additionally, software program problems can impede the device's programs, resulting in operational inadequacies.
Inconsistent product circulation is another essential issue. This can occur from variants in item weight, form, or size, which may affect the machine's capacity to manage items precisely. Insufficient training of drivers can intensify these issues, as inexperienced personnel might not recognize very early indicators of malfunction or might misuse the devices.
Resolving these usual packaging device issues quickly is vital to maintaining efficiency and ensuring a smooth operation. Normal inspections and proactive upkeep can substantially alleviate these issues, promoting a trustworthy packaging setting.
Tips for Lessening Downtime
To minimize downtime in packaging procedures, carrying out an aggressive maintenance method is vital. Frequently set up maintenance checks can identify potential problems prior to they rise, guaranteeing machines run efficiently. Establishing a regimen that includes lubrication, calibration, and assessment my company of vital parts can substantially decrease the regularity of unanticipated break downs.
Training staff to run machinery properly and acknowledge early caution signs of breakdown can also play an essential role. Equipping drivers with the expertise to carry out basic troubleshooting can stop small problems from creating significant hold-ups. Maintaining an efficient stock of essential spare components can speed up repair work, as waiting for parts can lead to extended downtime.
Furthermore, documenting machine efficiency and maintenance activities can assist recognize patterns and reoccurring troubles, permitting targeted treatments. Integrating advanced tracking technologies can give real-time information, enabling anticipating upkeep and minimizing the danger of abrupt failures.
Finally, cultivating open communication in between operators and maintenance groups ensures that any type of irregularities are promptly reported and addressed. By taking these aggressive measures, services can improve functional effectiveness and dramatically decrease downtime in packaging processes.
Choosing the Right Repair Solution
Selecting the appropriate repair service for product packaging machines is a vital choice that can considerably influence operational effectiveness. Begin by assessing the provider's experience with your particular kind of product packaging tools.
Following, consider the company's online reputation. Seeking responses from various other services within your industry can offer understandings into integrity and quality. Qualifications and collaborations with recognized equipment manufacturers can likewise indicate a commitment to quality.
Additionally, analyze their action time and accessibility. A company who can supply timely support decreases downtime and keeps production circulation stable. It's additionally critical to inquire about warranty and service guarantees, which can reflect the self-confidence the company has in their job.

Final Thought
In conclusion, the value of quick and reputable packaging equipment repair services can not be overstated, as they play a vital duty in decreasing downtime and making sure operational performance. Applying positive upkeep methods page and spending in staff training further improves the longevity of product packaging equipment.
Prompt repair services of packaging devices are important for maintaining functional effectiveness and decreasing downtime.Additionally, prompt repair services contribute to the long life of product packaging machinery. In general, the benefits try this web-site of involving dependable solution companies extend beyond instant repair work, favorably impacting the entire operational process of packaging procedures.
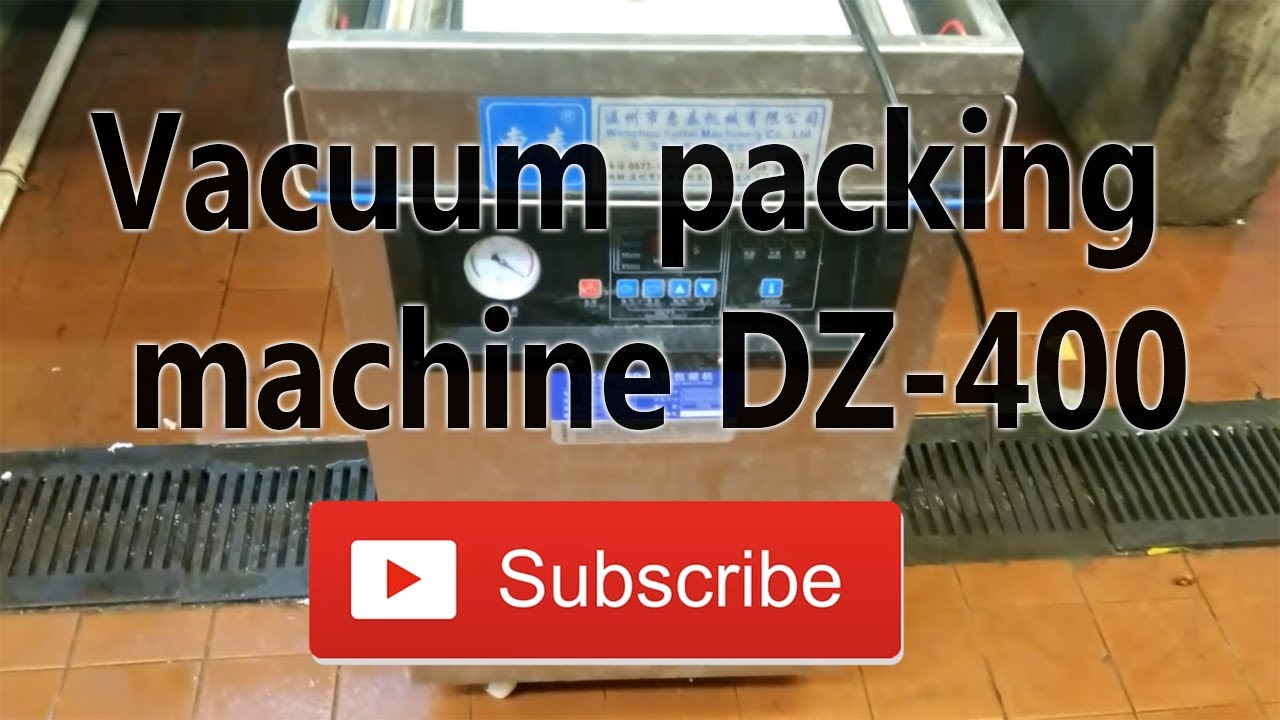
Report this page